Quality control is one of the most critical aspects of any construction project. Whether you’re overseeing a small home renovation or managing a large-scale luxury remodel, ensuring that every detail meets the highest standards is essential. Effective quality control not only enhances the durability and aesthetics of the project but also helps in maintaining client satisfaction and preventing costly rework. In this article, we’ll explore how to ensure quality control in your construction project, with a particular focus on the importance of clear construction contracts and the meticulous standards upheld by Pristine Luxury Remodeling.
The Foundation of Quality Control: Detailed Construction Contracts
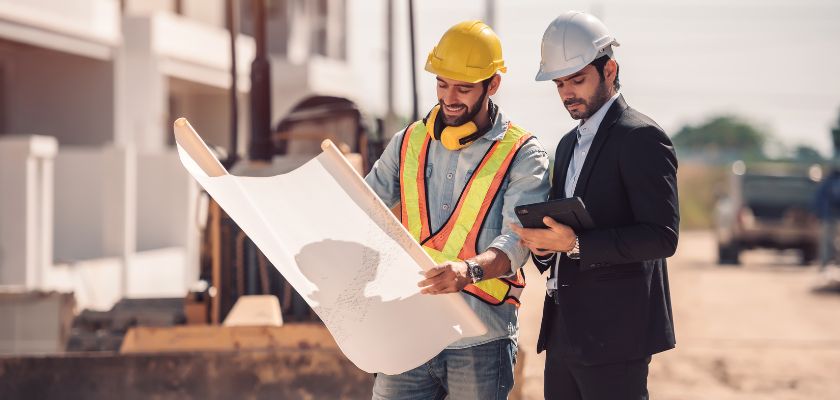
Quality control begins long before the first brick is laid; it starts with the creation of a detailed and well-structured construction contract. A construction contract is the foundation upon which the entire project is built, outlining the expectations, responsibilities, and standards that all parties must adhere to.
Defining Scope and Specifications
A comprehensive construction contract should clearly define the scope of work and specifications. This includes a detailed description of all tasks, materials, and workmanship standards required to complete the project. By explicitly stating these details, you ensure that everyone involved understands what is expected.
- Task Breakdown: The contract should include a breakdown of the tasks to be completed, along with deadlines for each phase. This not only helps in managing the timeline but also ensures that quality checks are performed at each stage.
- Material Specifications: Specify the types of materials to be used, including brands, quality grades, and sources. For high-end projects, such as those managed by Pristine Luxury Remodeling, the choice of materials is crucial, as they significantly impact the final look and feel of the project.
- Workmanship Standards: Clearly outline the expected level of craftsmanship. This includes standards for installations, finishes, and any custom work that may be part of the project. By setting these standards upfront, you can ensure that the finished product meets your expectations.
Establishing Quality Control Measures
Incorporating quality control measures into the construction contract is essential. These measures should include regular inspections, documentation requirements, and procedures for addressing any issues that arise during the project.
- Regular Inspections: The contract should specify when and how quality inspections will take place. Regular inspections help catch potential issues early, allowing for timely corrections and preventing more significant problems down the line.
- Documentation and Reporting: Require that all quality control measures be documented. This includes keeping records of inspections, materials used, and any deviations from the original plan. This documentation is invaluable in resolving disputes and ensuring accountability.
- Issue Resolution Procedures: Clearly outline the process for addressing any quality issues that arise. This should include steps for reporting the issue, determining responsibility, and implementing corrective actions.
Specifying Timelines and Milestones
A well-defined timeline is crucial for maintaining quality control throughout the project. The construction contract should include a detailed schedule with clear milestones that must be met before moving on to the next phase.
- Milestone Deadlines: Setting deadlines for key milestones ensures that the project progresses smoothly and that quality checks are completed before each new phase begins.
- Contingency Plans: Include contingency plans for potential delays. This could involve buffer time between milestones or alternative solutions for common issues that might arise during the project.
- Final Completion Date: The contract should specify a final completion date, including any penalties for delays. This helps keep the project on track and ensures that all quality control measures are completed within the agreed timeframe.
Implementing Quality Control on the Job Site
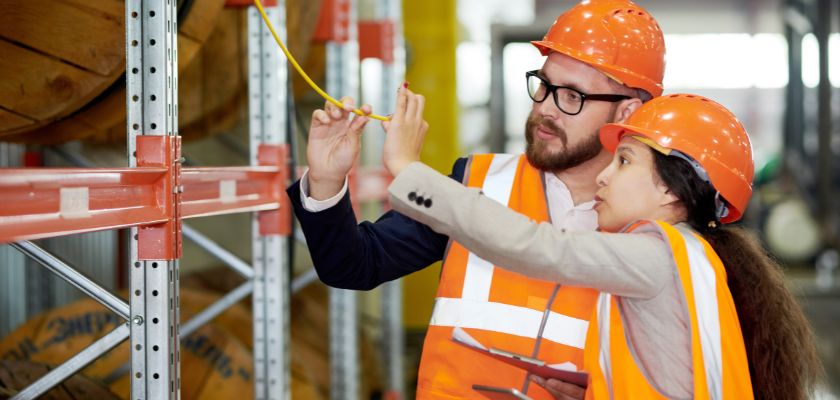
Once the project is underway, implementing effective quality control measures on the job site is critical. This involves close supervision, regular inspections, and clear communication among all parties involved.
On-Site Supervision and Management
Strong on-site supervision is key to maintaining quality control. A dedicated project manager or site supervisor should be responsible for overseeing the work, ensuring that it aligns with the specifications outlined in the construction contract.
- Daily Oversight: The project manager should conduct daily inspections to monitor progress and identify any potential quality issues. This proactive approach helps address problems before they escalate.
- Coordination with Contractors: The supervisor should maintain close communication with all contractors and subcontractors, ensuring that they understand the quality expectations and adhere to the project plan.
- Adherence to Safety Standards: Quality control also involves ensuring that all work is performed safely and in compliance with local regulations. The supervisor should monitor safety practices on-site to prevent accidents and ensure a smooth workflow.
Conducting Regular Quality Inspections
Regular quality inspections are essential for maintaining high standards throughout the project. These inspections should be conducted at key milestones and include a thorough review of the work completed.
- Pre-Milestone Inspections: Before any milestone is marked complete, conduct an inspection to ensure that all work meets the required standards. This includes checking for proper installation, adherence to specifications, and the quality of finishes.
- Material Inspections: Inspect all materials upon delivery to ensure they meet the specifications outlined in the construction contract. Reject any materials that do not meet the required standards to prevent issues later in the project.
- Final Walkthrough: Once the project is complete, conduct a final walkthrough with the client to review the work. This is an opportunity to address any concerns and ensure that all quality control measures have been met.
Ensuring Clear Communication
Clear communication is crucial for maintaining quality control. All parties involved, from the client to the contractors, should be kept informed of the project’s progress and any issues that arise.
- Regular Meetings: Schedule regular meetings with all stakeholders to discuss the project’s progress, address any issues, and make any necessary adjustments to the plan.
- Transparent Reporting: Provide transparent reports on the results of quality inspections and any corrective actions taken. This helps build trust and ensures that everyone is on the same page.
- Client Involvement: Involve the client in key decisions and inspections, especially in luxury projects like those managed by Pristine Luxury Remodeling. This ensures that the final product aligns with their vision and expectations.
Continuous Improvement and Final Quality Assurance
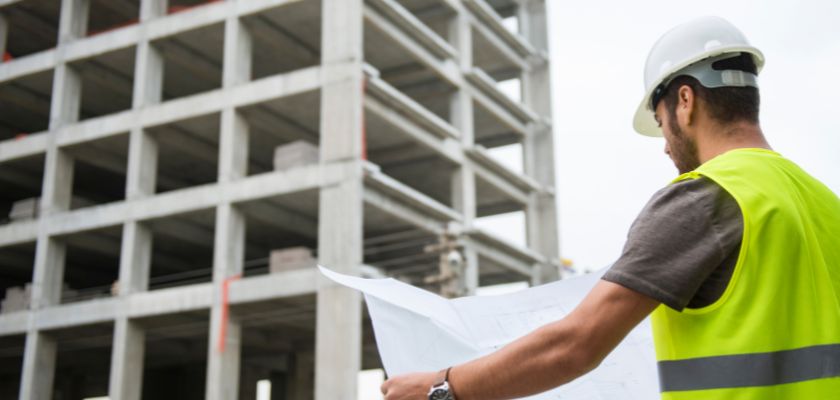
Quality control doesn’t end when the project is completed. Continuous improvement and final quality assurance are essential for delivering a finished product that meets the highest standards.
Learning from Past Projects
One of the best ways to improve quality control in future projects is to learn from past experiences. Conduct a post-project review to identify any areas where improvements can be made.
- Post-Project Review: After the project is completed, gather feedback from all stakeholders to evaluate what went well and where there were challenges. Use this information to refine your quality control processes for future projects.
- Documenting Lessons Learned: Document the lessons learned from each project and incorporate them into your standard operating procedures. This helps ensure that the same mistakes are not repeated and that best practices are consistently applied.
- Implementing Feedback: Use the feedback from clients and contractors to make continuous improvements. Whether it’s refining the construction contract or adjusting on-site supervision practices, this feedback is invaluable for maintaining high standards.
Final Quality Assurance Checks
Before handing over the completed project to the client, conduct a final quality assurance check to ensure that everything meets the required standards.
- Detailed Inspection: Perform a detailed inspection of the entire project, checking for any remaining issues that need to be addressed. This includes verifying that all work has been completed to the specifications outlined in the construction contract.
- Client Walkthrough: Arrange a final walkthrough with the client to review the completed work. Address any final concerns they may have and ensure that they are satisfied with the result.
- Handover Documentation: Provide the client with all necessary documentation, including warranties, maintenance instructions, and final inspection reports. This ensures that they have all the information they need to maintain the quality of the work.
Maintaining Long-Term Quality
Quality control doesn’t end when the project is completed. Providing ongoing support and maintenance ensures that the quality of the work is maintained over time.
- Follow-Up Inspections: Schedule follow-up inspections after the project is completed to ensure that everything remains in good condition. This is especially important in luxury remodeling projects, where maintaining the quality of finishes and materials is critical.
- Client Support: Offer ongoing support to the client, including maintenance services and advice on how to care for the finished work. This helps maintain the quality of the project and ensures long-term client satisfaction.
- Warranty Compliance: Ensure that all work is completed in compliance with warranty requirements. This provides additional protection for the client and reinforces the quality of the work.
Final Wording
Ensuring quality control in a construction project requires a combination of meticulous planning, clear communication, and proactive management. By starting with a detailed construction contract and implementing robust on-site quality control measures, you can prevent issues before they arise and ensure that the finished product meets the highest standards. In luxury projects like those undertaken by Pristine Luxury Remodeling, maintaining quality control is essential for delivering results that exceed client expectations. Whether you’re managing a small renovation or a large-scale remodel, a commitment to quality control will help ensure the success of your project and the satisfaction of your clients.
FAQ’s
1. Why is a detailed construction contract crucial for quality control?
A detailed construction contract outlines the scope of work, material specifications, and quality standards, ensuring that all parties have clear expectations. This foundation is essential for maintaining high-quality work throughout the project.
2. How can regular inspections help in maintaining quality control?
Regular inspections allow project managers to identify and address any quality issues early in the construction process. This proactive approach helps prevent small problems from escalating and ensures that the project stays on track.
3. What role does on-site supervision play in quality control?
On-site supervision is critical for maintaining quality control. A dedicated supervisor ensures that all work aligns with the specifications outlined in the construction contract and that any issues are promptly addressed.
4. How does communication impact quality control in construction projects?
Clear communication among all stakeholders, including contractors and clients, is vital for maintaining quality control. Regular updates and transparent reporting help ensure that everyone is aligned and that any concerns are quickly resolved.
5. What should be included in a post-project review to improve quality control?
A post-project review should include feedback from all stakeholders, an evaluation of what went well, and identification of any challenges. This information is essential for refining quality control processes in future projects.